Mechanical Design Project (1) - Ergonomic Mold Storage Racks
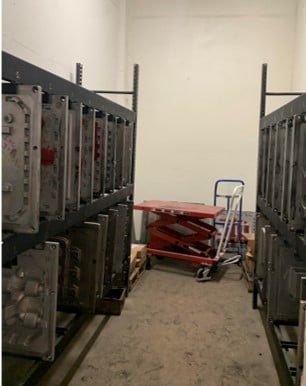
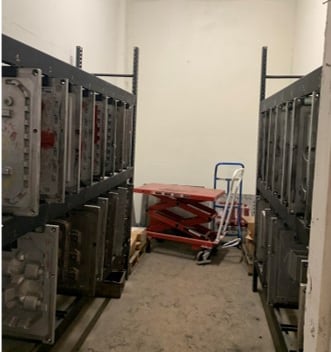
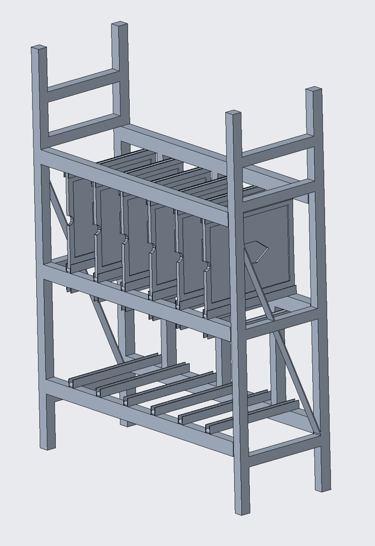
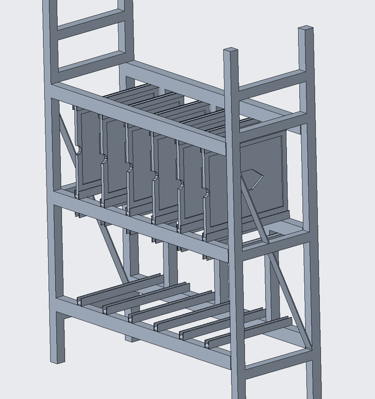
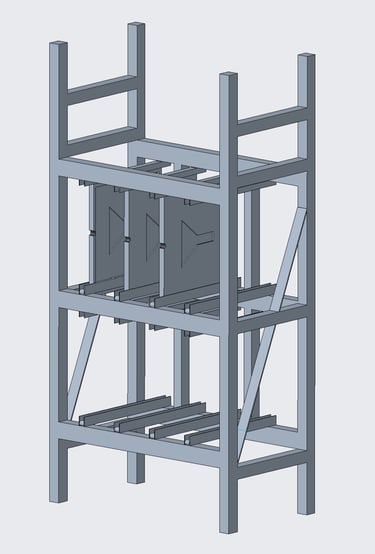

During my internship at G&W Electric Co., I was given two main projects to complete. The first is the stored molds racking project, which took place in G&W Electric's foundry (Manufacturer's Brass and Aluminum Foundry) in Blue Island, IL. This project focused on utilizing space in two "horse-stable" like rooms in the foundry by implementing new mold racks. I began this project by getting the dimensions of the room with a measuring tape, which is necessary for an engineering drawing to be made. After analyzing the rooms, I believed it would be most beneficial to implement two large racks (on each side) and one smaller rack (at the back of the room) for each room. Soon after, I began designing both racks in Creo using the dimensions I measured. Comparing my first design with my final, I achieved $4,000 in savings from using long, metal chains across the racks to prevent the molds from rolling out instead of individual toggle clamps for each mold. Soon after creating a Bill of Materials, ordering the parts, and the parts arriving, assembly began. Additionally, I included 1" rollers for ease of insertion/exertion as well as railing walls to prevent the molds from falling/swaying. Due to time constraints and delayed shipping of the parts, I did not have enough time left to finalize the project during my internship, however, it is currently being constructed and fabricated by my coworkers I worked with on this project.
The top picture displays the previous layout of the "horse-stable" room, the middle two pictures display the larger (left) and shorter (right) racks with several mock molds in place, and the bottom picture displays the Creo room layout of the racks together, respectfully.
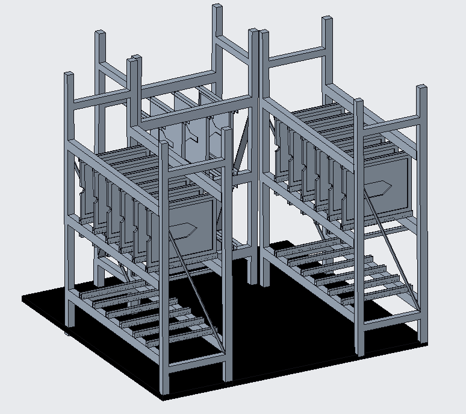
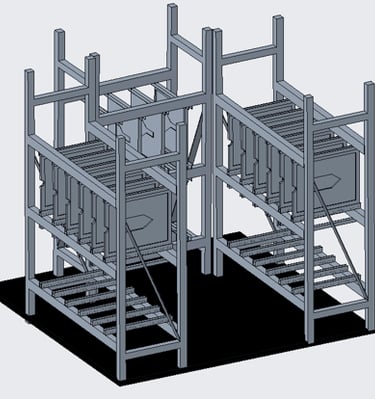
Mechanical Design Project (2) - Sinto Operating Platform
My second project during my internship at G&W Electric Co. focused on creating a more ergonomic operating platform for a $1.7 million molding machine (Sinto) in the company's foundry (MBAF). The operators have complained that they have been having difficulties accessing their cart since the current platform is not uniform and singular, which is essential to operate the machine. After measuring the dimensions of the working space and discussing with the operators, I began designing the platform using Creo. After designing the platform, I created a Bill of Materials, consulted with multiple steel vendors (achieved $1,000 in savings), and began assembly after receiving parts. Following the implementation of the platform, I revisited the foundry, and the operators were very happy with the result.
The top picture displays the Creo design I've created, and the bottom two pictures display the previous operating setup and the final implementation of the new platform, respectfully. As seen from the final implementation picture, the operator's cart is much more accessible, which will increase worker efficiency and production.
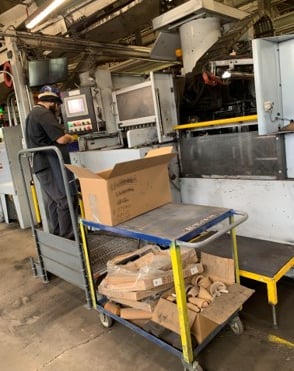
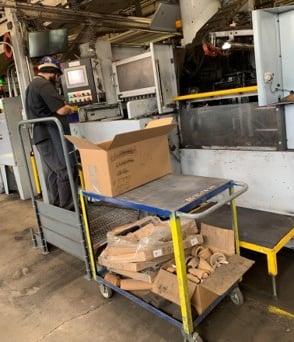
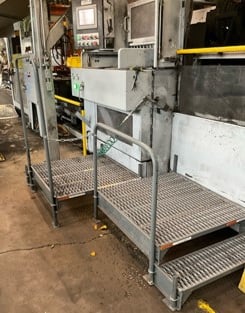
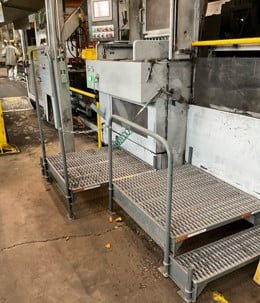
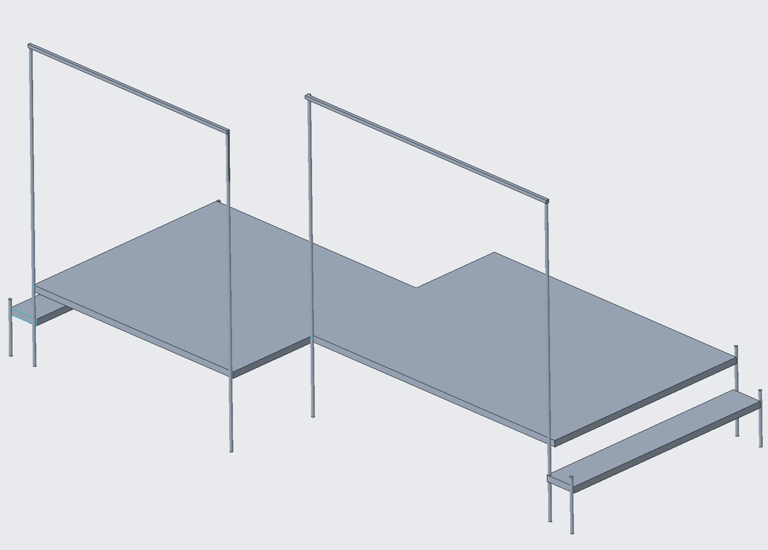
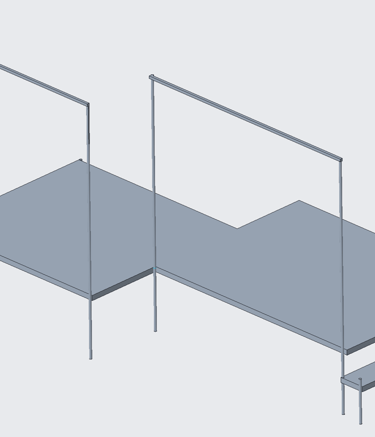
Location
Explore the manufacturing environment where I worked on the previous 2 projects and gained valuable experience in mechanical engineering
Mechanical Design Project (3) - Lapster
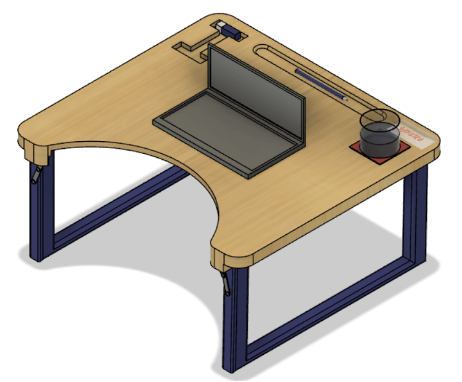
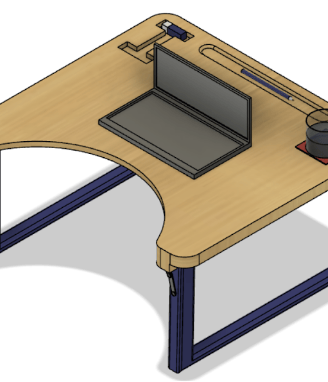
During my first semester in college, I designed a portable lap desk with three other students in the course "ME 170 - Computer-Aided Design". The prompt of this project was to create something unique that appeals to the needs of everyday college students at UIUC. After brainstorming, drawing sketches, and utilizing a Pugh Matrix, we began designing (with Autodesk Fusion 360) the most efficient and ergonomic lap desk that we could possibly think of. Our end design was very sophisticated, and it even included working hinge mechanisms from joints and screws designed by our group.
The picture below displays our final computer-aided design of Lapster:
Attached below is a link to our final group project report for Lapster:
https://docs.google.com/document/d/1Mc7qvcx72vwyayAq4vsB3J-zN_LllqGqs297fr4ofds/edit?usp=sharing
Mechanical Design Project (4) - Repurposed Kerosene Lantern
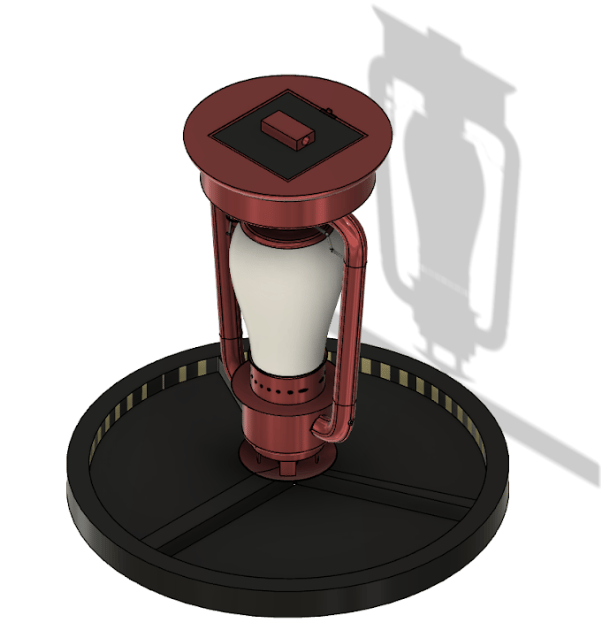
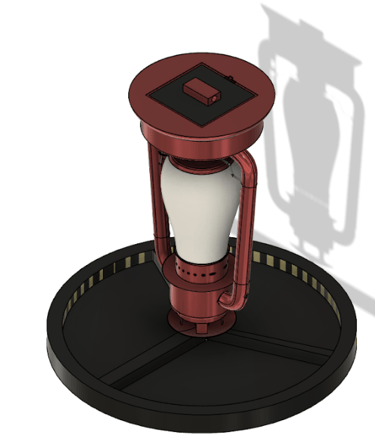
In the "ME 270 - Design for Manufacturability" course I took sophomore year, our individual final project was to engineer a dysfunctional object of our choice in our household into something with a new purpose. After finding an old, kerosene lantern in my basement, I chose to repurpose it into an innovative and stylish bird feeder. It would work by inserting bird feed through the bottom of the lantern (technically the top since it's flipped upside down), and it would dispense out the other end of the lantern onto a welded, evenly split 3-section plate attached to the bottom. Since the graders were impressed with my design and idea, I did great on this final project and ended with an A in the class.
The picture below displays my final computer-aided design of the repurposed lantern:
Attached below is the final project report for this repurposing project:
https://docs.google.com/document/d/1K2wxPDQJWAMcq27gMSsERWiBe3J0XD2nPWZ_YphnuHA/edit?usp=sharing
Mechanical Design Project (5) - Innovative Wrench Design
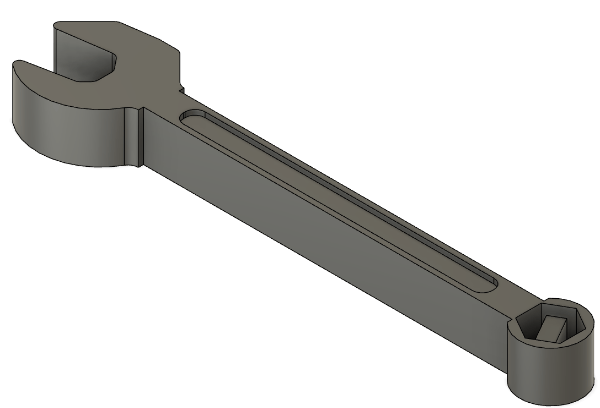
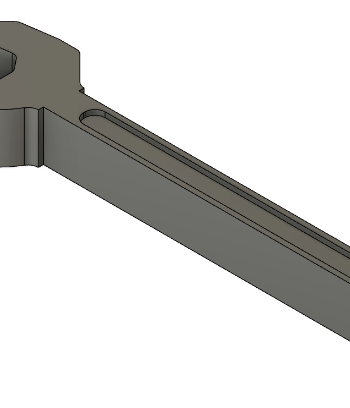
Another project I completed in the "ME 270 - Design for Manufacturability" course was the CAD design project with an analysis of it in UltiMaker Cura. This project focused on designing (in Autodesk Fusion 360) an innovative object of our choice and using UltiMaker Cura to decide which orientation would be best to 3D print it.
The pictures below display my final computer-aided design of the wrench:
An important aspect of 3D printing is designing the object to be easily created with a 3D printer with the proper orientation. If the object contains sharp corners, thin walls, or a stair-stepping effect, then the printed object's quality can be significantly worsened. This project helped students to see how design has a big impact on the manufacturing process.
The pictures below display my UltiMaker Cura orientation for the wrench to ensure a high-quality print:
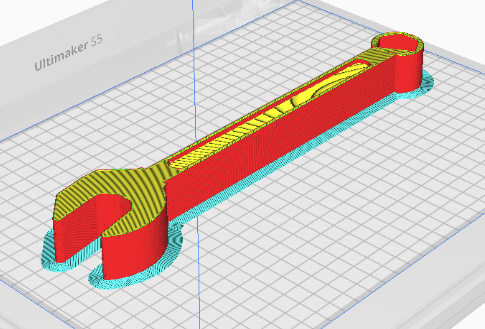
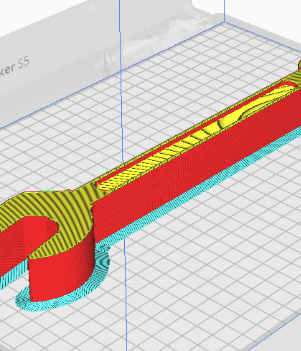
Attached below is the full report for this project:
https://docs.google.com/document/d/14ZxtaVUZ2M0nJm2xTuSttburvfB2JkX5IsXDmZCMRU4/edit?usp=sharing
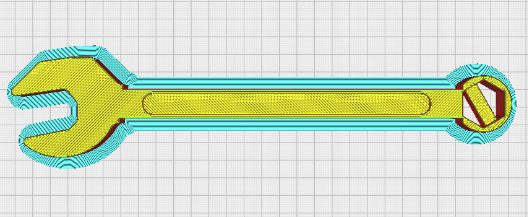
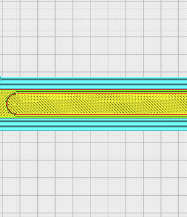
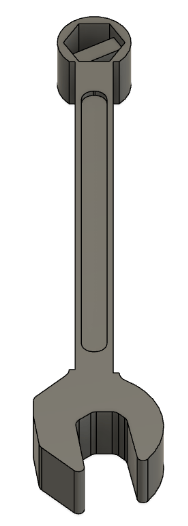
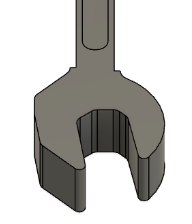
Mechanical Design Project (6) - 3D Printed Toy Car
This project aimed at enhancing our 3D printing skills (FDM) using UltiMaker Cura. At the Jackson Innovation Studio in the Sydney Lu Mechanical Engineering Building, several high-tech 3D printers have been recently installed, which has allowed us to design and create more intricate objects. The way I intended to design the car (in Fusion 360) was to first create the body with a curved slope, then to add holes that cut all the way through for axles to fit with the wheels attached on each side.
The pictures below display the toy car without the axles/wheels and the final 3D printed toy car, respectively.
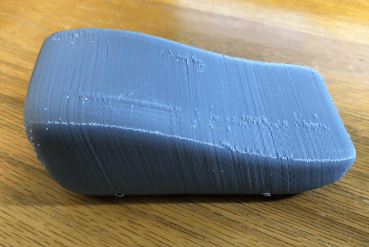
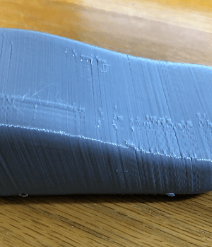
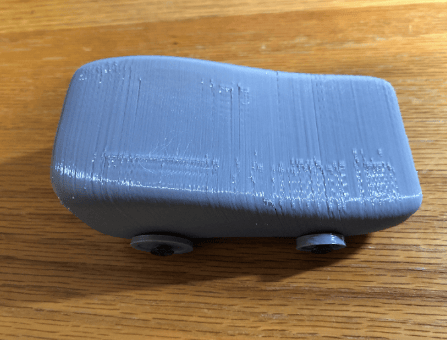
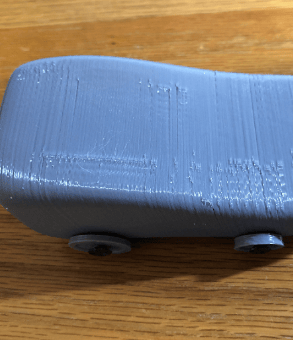
Location
Explore the manufacturing environment where I worked on the previous 4 projects and gained valuable experience in mechanical engineering
Welding
This past summer during my internship, I had the amazing opportunity to work in the fabrication apprenticeship program at G&W Electric Co. Every Tuesday and Thursday, I would participate with the apprentices and learn about metal fabrication, stick welding, brazing, and more. Scott Erickson also instructed me one-on-one at G&W Electric Co., a skilled welder who has worked at the company for many years and even teaches as a welding professor at Morton college. Steve Gilbert, another skilled professional at G&W Electric, was another teacher that taught the apprenticeship classes.
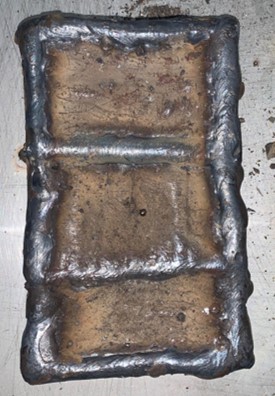
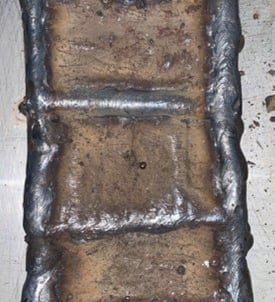
Apprenticeship Project 1: 3 Stairsteps
This project focused on developing our straight weld lines across a surface. As seen from the pictures to the right, each "level" is slightly higher than the previous. Additionally, we were instructed to alternate the weld direction for each step. For example, the weld lines for first step run from right to left, the second step up and down, and the third step back to right to left.
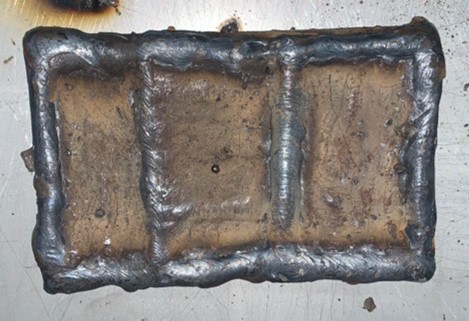
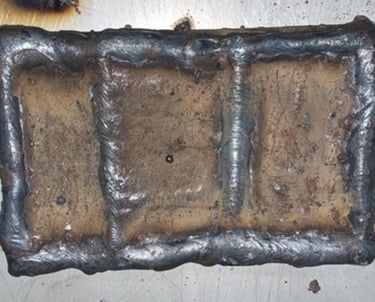
Apprenticeship Project 2: T-Joint
This project focused on perfecting a T-joint weld and ensuring the connecting piece is straight, even, and sturdy.
Welding Video on Sinto Platform (see Mechanical Design Project 2 above)
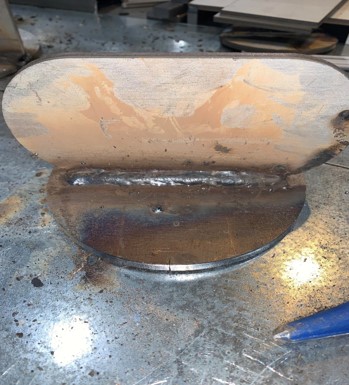
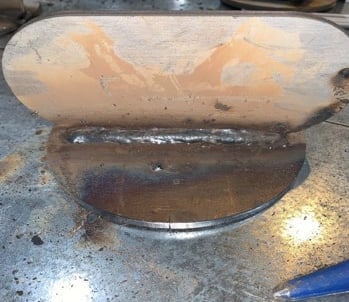
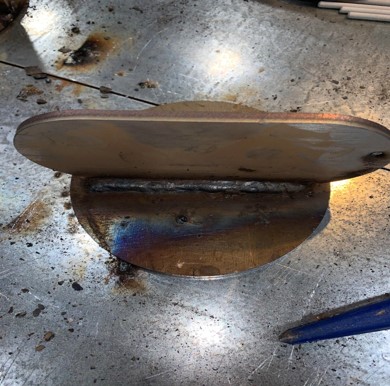
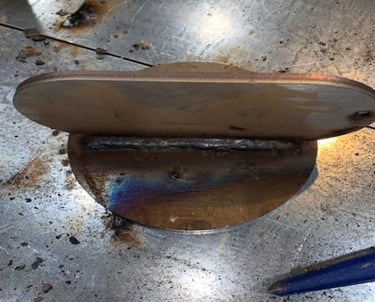
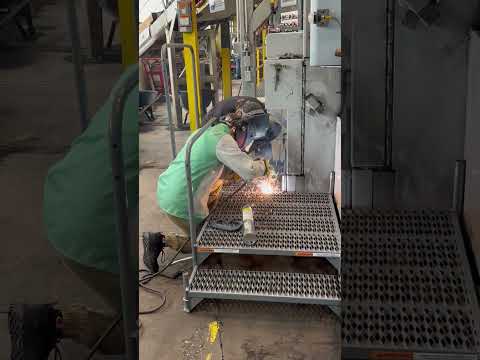